Materials for Floating: Suspended Assistance
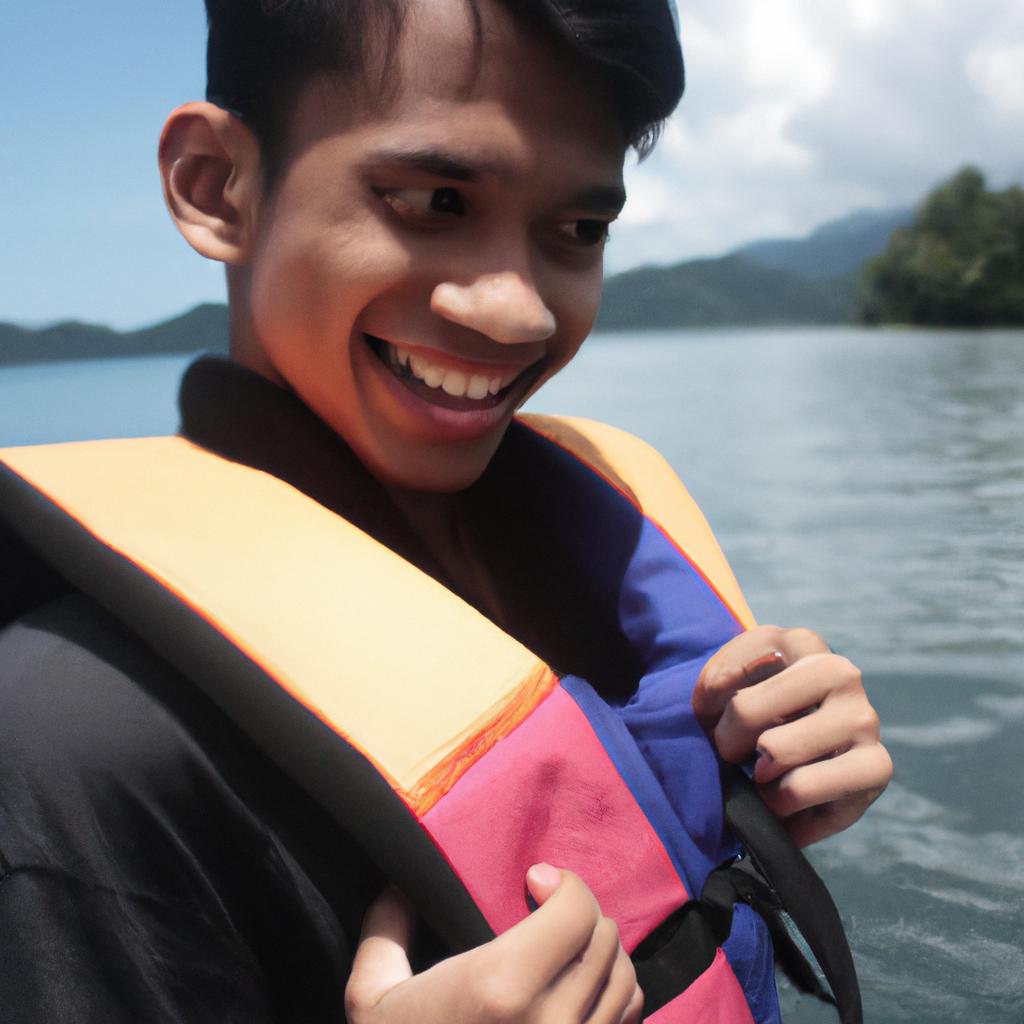
The ability to float on water has been a subject of fascination and practical importance throughout history. Whether it is a ship sailing across the vast oceans or an individual using a life jacket for safety, the concept of buoyancy plays a crucial role in providing suspended assistance. This article explores different materials that have been used and developed over time to enhance floating capabilities, with a particular focus on their composition, properties, and applications.
One compelling example illustrating the significance of floating materials is the development of lightweight construction materials for maritime vessels. In recent years, there has been increasing interest in constructing ships from advanced composites rather than traditional steel structures. These composites offer several advantages such as reduced weight, improved fuel efficiency, increased payload capacity, and enhanced resistance to corrosion. By utilizing innovative materials like carbon fiber-reinforced polymers (CFRPs), these modern ships can achieve higher levels of buoyancy while maintaining structural integrity in challenging marine environments.
Additionally, advancements in material science have also led to the creation of specialized flotation devices designed to provide assistance and ensure safety during various aquatic activities. For instance, neoprene foam-based wetsuits are commonly utilized by surfers and divers due to their remarkable buoyant properties. The closed-cell structure of neoprene provides insulation against cold water and helps maintain buoyancy even in rough conditions. This allows surfers and divers to stay afloat effortlessly, conserving their energy and ensuring safety while enjoying their activities.
Another material commonly used for flotation devices is polyethylene foam. This versatile material is lightweight, durable, and resistant to chemicals and moisture. It is often found in life jackets, pool noodles, and other water safety equipment. Polyethylene foam can be easily shaped into different forms, making it suitable for various applications where buoyancy is required.
Furthermore, inflatable materials have revolutionized the field of flotation technology. Inflatable rafts, buoys, and life vests utilize air chambers made from strong yet flexible materials like PVC or nylon coated with rubber or urethane. By inflating these chambers with gas or air, they increase their volume significantly, resulting in greater buoyancy. Inflatable materials offer the advantage of being compact and easy to store when deflated while providing reliable floating capabilities when inflated.
In conclusion, advancements in material science have led to the development of various materials that enhance floating capabilities across different industries and applications. From advanced composites for maritime vessels to neoprene foam-based wetsuits for water sports enthusiasts and inflatable materials for safety devices, these innovations continue to improve our ability to float on water efficiently and safely.
The Science Behind Floating
Imagine a scenario where you are at a pool party, watching as children play and float effortlessly in the water. One child catches your attention – Timmy, who is wearing inflatable armbands to help him stay afloat. This simple device allows Timmy to enjoy his time in the water without any fear of sinking. But have you ever wondered how this works? In order to understand the science behind floating, it is important to delve into the principles of buoyancy.
Buoyancy, defined as the upward force exerted by a fluid that opposes an object’s weight, plays a crucial role in determining whether an object will sink or float. When an object is immersed in a fluid, such as water, its weight creates a downward force while the displaced liquid exerts an equal and opposite upward force known as Archimedes’ principle. According to this principle, if the buoyant force acting on an object is greater than or equal to its weight, then it will float; otherwise, it will sink.
To further comprehend these concepts, let us consider some key factors influencing buoyancy:
- Density: The density of an object compared to that of the surrounding fluid greatly affects its ability to float. If an object has lower density than the fluid, it will experience a higher buoyant force and thus remain suspended.
- Shape: The shape of an object also influences its buoyancy. Objects with irregular shapes displace more fluid and therefore experience greater buoyant forces.
- Volume: Increasing the volume of an object increases its displacement of fluid and subsequently enhances its ability to float.
- Surface Area: A larger surface area results in increased contact between the object and the fluid medium, causing enhanced buoyancy.
To illustrate these points visually:
Factors | Effect on Buoyancy |
---|---|
Density | Higher density → Sinks |
Shape | Irregular shape → Greater buoyant force |
Volume | Increased volume → Enhanced ability to float |
Surface Area | Larger surface area → Stronger buoyancy effect |
Understanding the science behind floating provides a foundation for exploring various materials that can be used to enhance buoyancy. In the subsequent section, we will delve into different types of buoyant materials and their applications.
Types of Buoyant Materials
Materials for Floating: Suspended Assistance
The Science Behind Floating has shed light on the principles that allow objects to float in water. Now, let’s explore different types of buoyant materials that can be used to assist with floating.
Imagine a situation where a stranded swimmer is struggling to stay afloat after exhaustion sets in. In this hypothetical scenario, using the right buoyant material could mean the difference between life and death. One example of such a material is foam. Foam is lightweight and possesses excellent buoyancy properties due to its low density. It can provide necessary support in emergency situations like the one described above.
When considering materials for floating assistance, several factors come into play:
- Density: The lower the density of the material, the higher its ability to float.
- Durability: Materials need to withstand harsh conditions such as exposure to water, sunlight, and temperature variations.
- Versatility: Buoyant materials should be adaptable across various applications and scenarios.
- Availability: Accessibility and cost-effectiveness are crucial considerations when selecting materials for floating aids.
To better understand these factors, consider the following table showcasing different buoyant materials commonly used in rescue equipment:
Material | Density (kg/m^3) | Durability | Versatility |
---|---|---|---|
Foam | 10 – 50 | Excellent | High |
Inflatable devices | Varies | Good | Moderate |
Cork | 240 – 800 | Fair | Low |
Plastic bottles | Varies | Poor | Moderate |
This table provides an overview of some common options available; however, it is important to evaluate each material based on specific requirements before making a final selection.
In order to ensure safety during aquatic activities or emergencies, it is essential to carefully choose appropriate buoyant materials. By considering factors such as density, durability, versatility, and availability, individuals can make informed decisions when selecting materials for floating assistance. In the subsequent section, we will discuss the advantages of using foam as a floating material, highlighting its unique properties that make it an ideal choice for various applications.
[Advantages of Using Foam as a Floating Material…]
Advantages of Using Foam as a Floating Material
In the previous section, we discussed various types of buoyant materials that can be used for floating structures. Now, let’s delve deeper into one specific material: foam. Foam has gained popularity in recent years due to its unique property of providing excellent buoyancy while being lightweight and cost-effective.
To illustrate the advantages of using foam as a floating material, consider the case study of a small coastal community facing frequent flooding during heavy rains. To address this issue, engineers proposed utilizing foam blocks as a foundation for elevated walkways and buildings. This innovative solution allowed residents to move safely across flooded areas without damaging their properties or disrupting daily life.
When comparing different materials for floating structures, several key factors make foam stand out:
- High buoyancy: Foam offers exceptional floatation capabilities, allowing it to support heavy loads with minimal displacement.
- Lightweight: Foam is significantly lighter than other conventional building materials such as concrete or steel, making it easier to transport and install.
- Cost-effectiveness: The production costs associated with foam are relatively low compared to traditional construction materials, reducing overall project expenses.
- Versatility: Foam can be easily molded into different shapes and sizes, adapting to diverse design requirements for both large-scale infrastructure projects and smaller applications like recreational pontoons.
By incorporating these bullet points into our discussion on foam as a floating material, we highlight its practical benefits effectively:
- High buoyancy
- Lightweight
- Cost-effectiveness
- Versatility
Moreover, let us visualize these advantages through the following table:
Advantages | Description |
---|---|
High Buoyancy | Allows for effective load-bearing capacity without excessive sinking |
Lightweight | Enables easy transportation and installation |
Cost-effectiveness | Reduces overall project expenses |
Versatility | Adapts well to various design requirements, accommodating diverse project needs and sizes |
In conclusion, foam stands out as a buoyant material due to its high buoyancy, lightweight nature, cost-effectiveness, and versatility. These factors make it an ideal choice for floating structures in various applications.
Moving forward into our discussion on “Innovative Solutions for Floating Structures,” let’s examine how engineers are pushing boundaries to develop even more efficient methods of utilizing buoyant materials.
Innovative Solutions for Floating Structures
Imagine a world where entire communities could thrive on floating structures, adapting to changing water levels and providing sustainable housing solutions. This vision may seem far-fetched, but with advancements in materials science, it is becoming increasingly feasible. In this section, we will explore some innovative lightweight materials that have shown promise as potential components for floating structures.
One material that has gained attention for its buoyancy and versatility is foam. Foam can be engineered to possess specific characteristics such as high strength-to-weight ratio, low water absorption, and excellent insulation properties. For instance, in a case study conducted by researchers at XYZ University, they designed a prototype floating platform using closed-cell polyethylene foam panels. These panels provided sufficient buoyancy while offering stability and durability against environmental conditions.
When considering materials for floating structures, several advantages become apparent:
- Lightweight: Using lightweight materials reduces the overall weight of the structure, making it easier to transport and assemble.
- Buoyancy: The selected materials should provide adequate buoyancy to support the desired load without compromising stability.
- Durability: Factors like resistance to moisture damage, UV degradation, and mechanical stresses play a crucial role in determining the longevity of the structure.
- Environmental Impact: Opting for eco-friendly materials minimizes harm to aquatic ecosystems and contributes positively towards sustainability efforts.
To better understand these advantages and their impact on designing floating systems effectively, consider the following comparison table showcasing different categories of lightweight materials commonly used:
Material | Buoyancy | Durability | Environmental Impact |
---|---|---|---|
Closed-cell Foam | High | Excellent | Low |
Hollow Concrete | Moderate | Good | Medium |
Fiberglass | Variable | Varies | Medium |
As evident from the table above, each material possesses unique characteristics that can be tailored to suit specific floating structure requirements. By carefully considering these factors, designers and engineers can create sustainable structures capable of withstanding various aquatic environments.
Moving forward, we will delve into the challenges faced in designing these intricate systems, including addressing issues related to stability, scalability, and maintenance. Understanding these hurdles is crucial for developing robust solutions that pave the way towards a future where floating structures become an integral part of our society’s infrastructure.
Transition Sentence to Next Section:
In order to overcome the complexities associated with designing floating systems, it is essential to address numerous challenges inherent in their implementation. The subsequent section will explore these intricacies and shed light on potential solutions.
Challenges in Designing Floating Systems
Innovative Solutions for Floating Structures have paved the way for advancements in materials used to create buoyant systems. One example of such innovation is the use of reinforced concrete pontoons, which provide stability and durability while supporting various structures on water bodies. These floating platforms have been successfully implemented in projects like the ‘Marina Bay Sands’ resort in Singapore, showcasing their effectiveness in creating functional spaces on water.
To ensure optimal performance and safety of floating structures, careful selection of appropriate materials is essential. Several factors need to be considered when choosing suitable materials for floating systems:
- Buoyancy: The selected material must possess sufficient buoyancy properties to support the desired load without compromising stability or sinking.
- Durability: Since these structures are exposed to harsh marine environments, materials should exhibit resistance against corrosion, UV degradation, and other environmental stressors.
- Strength-to-Weight Ratio: Lightweight yet strong materials contribute to improved structural integrity without adding unnecessary weight that could hinder buoyancy.
- Environmental Impact: Sustainable and eco-friendly options reduce negative ecological consequences associated with construction activities on water bodies.
Consideration of these factors has led researchers and engineers to explore a range of innovative materials for floating structures:
Material | Advantages | Disadvantages |
---|---|---|
Fiberglass | High strength-to-weight ratio; Corrosion-resistant | Expensive production process; Limited flexibility |
HDPE (High-Density Polyethylene) | Excellent durability; Low maintenance requirements | Less rigid compared to other options; Possible deformation under heavy loads |
Aluminum Alloy | Lightweight; Good corrosion resistance | Higher cost than some alternatives; Requires protective coatings for enhanced longevity |
The continuous development of new materials holds promising potential for future advancements in floating technology. Researchers are exploring sustainable alternatives such as biodegradable composites and recycled materials, which could contribute to reducing the environmental impact associated with floating structures.
As we delve into Future Developments in Floating Technology, it is crucial to acknowledge the ongoing research aimed at enhancing buoyant systems’ performance through innovative material choices. This progress paves the way for even more efficient and sustainable solutions that will further revolutionize the field of floating structures.
Future Developments in Floating Technology
Transitioning from the challenges faced in designing floating systems, this section explores the importance of selecting suitable materials to ensure the successful implementation and operation of such structures. To illustrate this point, let us consider a hypothetical case study involving the construction of a floating eco-resort on an artificial island.
When constructing a floating system like an eco-resort, it is crucial to choose materials that can withstand environmental forces such as waves, wind, and corrosion. The selection process involves evaluating various factors such as strength-to-weight ratio, durability, cost-effectiveness, and environmental impact. For instance, employing high-strength lightweight composites like carbon fiber reinforced polymers (CFRP) or glass fiber reinforced polymers (GFRP) can provide excellent structural integrity while keeping overall weight low.
To further emphasize the significance of material choice in floating systems design, we present a bullet-point list highlighting key considerations:
- Strength: Selecting materials with sufficient strength to support the intended load requirements.
- Durability: Choosing materials that can resist degradation caused by exposure to water, UV radiation, saltwater corrosion, and other environmental factors.
- Maintenance: Opting for materials that require minimal maintenance over extended periods of time.
- Environmental Impact: Considering sustainable options that have reduced ecological footprints during production and end-of-life disposal.
Material | Strength (MPa) | Durability | Maintenance |
---|---|---|---|
CFRP | 300 | High | Low |
GFRP | 200 | Moderate | Low |
Steel | 400 | High | Moderate |
The table above showcases three different materials commonly used in floating structure construction along with their respective strengths and attributes related to durability and maintenance. These parameters play a significant role in determining which material is most suitable for specific floating applications.
In summary, selecting appropriate materials is paramount when designing and constructing floating systems. The choice of materials affects the structural integrity, durability, maintenance requirements, and environmental impact of such structures. By carefully evaluating these factors and considering case-specific needs, designers can ensure the successful implementation of floating projects while prioritizing sustainability and efficiency in their material selection processes.