Drag and Floating: Hydrodynamic Insights into Drag in the Context of Floating
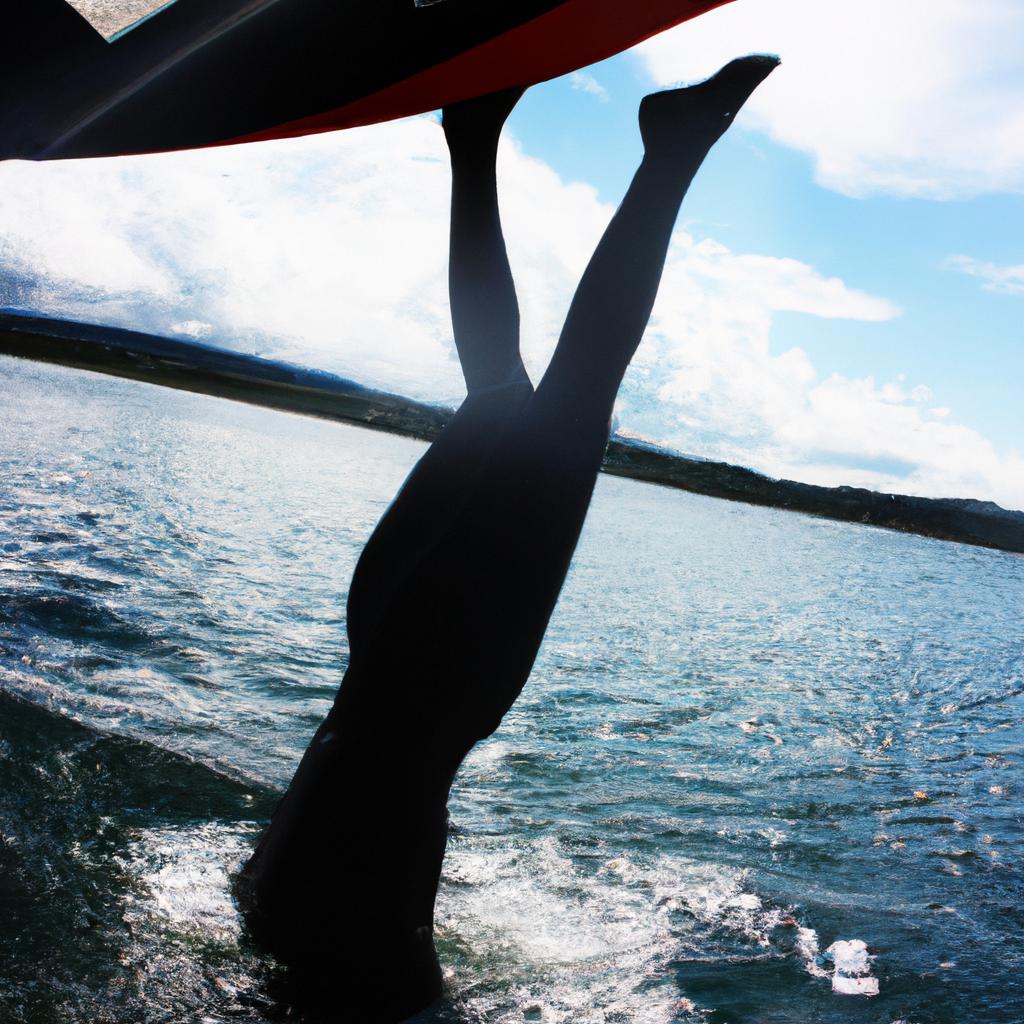
The study of drag and floating in the context of hydrodynamics provides valuable insights into the forces that act upon objects submerged or partially submerged in fluid. Understanding drag is crucial for various applications, including ship design, offshore engineering, and marine transportation. This article aims to explore the phenomenon of drag in the context of floating by examining relevant hydrodynamic principles and their implications.
Consider a hypothetical scenario where a large shipping vessel needs to navigate through rough seas. As waves crash against its hull, the ship experiences resistance due to drag, which hampers its speed and efficiency. To optimize performance and reduce fuel consumption, it becomes imperative to understand the factors governing drag forces on floating objects. By delving into the intricacies of hydrodynamics and analyzing concepts such as boundary layers, flow separation, and pressure distribution around floating bodies, we can gain valuable insights into how drag affects buoyant structures.
By investigating different aspects of drag in relation to floating entities, this article will shed light on fundamental hydrodynamic principles that govern these phenomena. Furthermore, it will delve into practical considerations such as wave-induced loads and vortex shedding effects that impact the behavior of floating structures. Through an academic exploration of these topics, readers will not only develop a deeper understanding of drag but also appreciate the importance of designing efficient and seaworthy structures that can withstand the forces exerted by water currents, waves, and other environmental factors.
Understanding Drag: A Brief Overview
Imagine a sailboat gliding through the water, its sails billowing in the wind. Despite the seemingly effortless motion, an invisible force is at play – drag. In order to comprehend the intricacies of drag and its impact on floating objects, it is essential to explore various aspects of this phenomenon.
To begin our exploration, let us consider a hypothetical scenario involving a streamlined boat moving swiftly along a river. As the boat accelerates, it encounters resistance from the surrounding medium – water. This resistance manifests itself as drag, which opposes the forward motion of the boat. The magnitude of drag depends on several factors, such as the speed of the object relative to its surroundings and the properties of both the object and its environment.
In order to gain further insight into these factors influencing drag, let us delve deeper into their significance:
- Shape: The shape of an object plays a crucial role in determining drag. Streamlined shapes with minimal surface area facing against flow tend to experience less drag compared to irregular or blunt shapes that disrupt fluid flow.
- Surface Texture: The roughness or smoothness of an object’s surface also affects drag. Rough surfaces create more turbulence within the surrounding fluid, increasing frictional forces and consequently enhancing drag.
- Fluid Viscosity: Different fluids possess varying levels of internal friction known as viscosity. Higher viscosity leads to increased resistance against movement through that particular fluid medium, resulting in higher amounts of drag.
- Object Size: The size of an object influences not only its exposure to external forces but also alters how fluid molecules interact with its surface area. Larger objects generally face greater opposition due to larger contact areas between their surfaces and flowing mediums.
This brief overview highlights some key elements contributing to drag experienced by floating objects. Understanding these factors allows for a better comprehension of why certain objects encounter different magnitudes of resistive forces when immersed in fluids like air or water. In the subsequent section, we will explore in detail how an object’s shape influences drag, shedding light on its significance in hydrodynamics.
The Role of Shape in Drag
Building upon our understanding of drag, let us now delve into the role of shape in this hydrodynamic phenomenon.
To illustrate the influence of shape on drag, consider a hypothetical scenario in which we have two objects – Object A and Object B. Both objects are identical in size and made from the same material, but they differ significantly in their shapes. Object A has a streamlined, aerodynamic shape with smooth contours, while Object B is irregularly shaped with many protrusions. When these two objects are subjected to an airflow, we would expect to observe variations in the drag forces acting upon them.
Shape plays a crucial role in determining drag due to several factors:
- Form Drag: The form or pressure drag arises from the resistance caused by the object’s frontal area exposed to flow. Objects with larger frontal areas experience higher form drag compared to those with smaller frontal areas.
- Skin Friction Drag: This type of drag results from the friction between the fluid and the surface of an object. Irregular shapes tend to disrupt laminar flow near their surfaces, leading to increased skin friction drag.
- Separation and Wake Drag: Objects with non-streamlined shapes often create turbulence as air flows around them. This turbulent wake behind such objects contributes to additional drag forces.
- Flow Attachment: The ability of an object’s shape to maintain attached flow can affect its overall drag profile. Smooth curves and gradual transitions promote better flow attachment than sharp edges or abrupt changes in geometry.
- Shape matters: It affects not only aesthetics but also performance.
- Streamlined designs reduce resistance and enhance efficiency.
- Complex shapes may lead to greater energy consumption.
- Understanding how different shapes interact with fluids aids design optimization.
Table representing characteristics influencing shape-drag relationship:
Characteristic | Description | Impact on Drag |
---|---|---|
Frontal Area | The area of an object perpendicular to the flow direction. | Larger frontal areas result in higher form drag. |
Surface Smoothness | The smoothness or roughness of an object’s surface. | Rough surfaces increase skin friction drag. |
Flow Separation | Occurs when airflow detaches from an object’s surface. | Separated flows contribute to additional wake drag. |
Geometric Features | Shapes and contours defining an object’s overall geometry. | Sharp edges may disrupt flow attachment, increasing drag. |
As we can see, shape has a profound impact on the drag experienced by floating objects. By considering these factors, engineers and designers can optimize shapes to minimize resistance and enhance performance across various applications such as ship hulls, aircraft wings, and even sporting equipment like racing cars or bicycles.
Understanding how shape influences drag leads us to explore another crucial aspect – the influence of surface roughness on this hydrodynamic phenomenon
Surface Roughness and its Impact on Drag
Transitioning smoothly from the previous section on the role of shape in drag, we now turn our attention towards another factor that significantly impacts drag – surface roughness. To illustrate this concept, let’s consider a hypothetical scenario where two identical objects are floating in water: one with a perfectly smooth surface and the other with a rough texture.
Surface roughness plays a crucial role in determining the level of drag experienced by an object. When an object has a rough surface, it disrupts the flow of water around it, causing turbulence and increasing resistance. This increased resistance leads to higher drag forces acting upon the object, ultimately impeding its motion through the fluid.
To gain a deeper understanding of how surface roughness affects drag, let us explore some key points:
- Increased friction: A rough surface creates more contact points between the flowing fluid and the object. This increased interaction results in higher frictional forces, intensifying the drag experienced by the object.
- Vortex shedding: The irregularities on a rough surface can cause vortices to form as fluid flows past them. These vortices contribute to additional energy losses and increase overall drag.
- Boundary layer separation: Surface irregularities also disturb the boundary layer—the thin layer of fluid adjacent to the object’s surface—leading to separation. This phenomenon generates larger areas of low-pressure zones behind an object, which further amplifies drag.
- Drag coefficient variation: The presence of surface roughness alters the value of the drag coefficient for an object. In general, objects with smoother surfaces tend to have lower drag coefficients compared to those with significant levels of roughness.
To visually comprehend these effects, refer to Table 1 below:
Surface Condition | Drag Coefficient (Cd) |
---|---|
Smooth | 0.2 |
Moderately Rough | 0.4 |
Rough | 0.6 |
Very Rough | 0.8 |
Table 1: Drag coefficients for different surface conditions
As demonstrated in Table 1, the drag coefficient increases as the level of surface roughness intensifies. This information highlights the importance of minimizing surface irregularities when designing objects intended to float with minimal resistance.
In summary, surface roughness significantly influences drag by increasing friction, promoting vortex shedding and boundary layer separation while also affecting the object’s drag coefficient value. Understanding these effects allows engineers and designers to optimize shapes and surfaces for reduced drag in various floating applications.
Transitioning smoothly into our next section on “The Influence of Velocity on Drag,” we delve further into the complex relationship between fluid flow velocity and drag forces acting upon floating objects.
The Influence of Velocity on Drag
Surface roughness plays a crucial role in determining the level of drag experienced by floating objects. As we have discussed earlier, small irregularities on the surface of an object can significantly affect its hydrodynamics. To further explore this relationship between surface roughness and drag, let us consider the example of a ship navigating through ocean waters.
Imagine a scenario where two ships with identical dimensions and shapes are sailing side by side. However, one of the ships has a smooth hull while the other has a hull covered in barnacles and algae. Due to the presence of these marine organisms, the second ship’s hull is considerably rougher than that of the first ship. Now, as both vessels move forward at similar speeds, they will experience different levels of drag due to their contrasting surface conditions.
To understand why this happens, let us delve into some key factors related to surface roughness and its impact on drag:
- Increased friction: The uneven surface caused by roughness creates more contact points between water molecules and the object’s surface. This increased contact leads to higher frictional forces acting against the movement of the object through water.
- Turbulence generation: Surface irregularities disrupt the smooth flow of water around an object, creating localized turbulence zones. These turbulent eddies increase resistance and result in additional drag.
- Separation and reattachment: Rough surfaces tend to cause flow separation from certain areas of an object’s surface, followed by reattachment downstream. This phenomenon results in vortices forming behind the object, causing additional drag.
- Pressure variations: Irregularities on an object’s surface lead to non-uniform pressure distribution along its length, resulting in varying magnitudes of drag at different sections.
To illustrate these concepts further, consider Table 1 below which compares various aspects related to drag for smooth versus rough surfaces:
Table 1: Comparison Between Smooth and Rough Surfaces
Aspect | Smooth Surface | Rough Surface |
---|---|---|
Frictional Drag | Low | High |
Turbulence Generation | Minimal | Significant |
Separation and Reattachment | Limited | Pronounced |
Pressure Distribution | Uniform | Non-Uniform |
As we can see from this table, surface roughness has a substantial impact on the drag experienced by floating objects. By understanding these hydrodynamic insights into drag, engineers and designers can develop strategies to minimize roughness-induced drag and enhance the overall efficiency of floating structures.
Moving forward, let us now explore another crucial aspect related to drag: the influence of velocity. Understanding how changes in velocity affect drag is vital for optimizing the performance of floating objects.
[Transition sentence] Now, let’s shift our focus towards examining the influence of velocity on drag as we delve into the concept of boundary layer and its effect on drag.
Boundary Layer and its Effect on Drag
Transitioning from the previous section’s exploration of velocity’s influence on drag, we now delve into the concept of boundary layer and its impact on drag. Understanding this phenomenon is crucial for comprehending how different factors affect drag when an object floats in a fluid medium.
To illustrate the significance of the boundary layer, let us consider a hypothetical scenario involving a ship navigating through water at high speeds. As the ship moves forward, it creates disturbances within the water that generate vortices near its surface. These vortices disrupt smooth flow around the ship’s hull, resulting in an increase in drag force.
The presence of a turbulent boundary layer can significantly contribute to increased drag. This boundary layer forms due to friction between the fluid and the surface of the floating object. Its thickness varies depending on several factors such as fluid viscosity, surface roughness, and flow conditions. A thicker boundary layer leads to higher skin friction drag, while a thinner one reduces resistance.
Understanding these hydrodynamic phenomena is essential for optimizing design choices when it comes to floating objects like ships or offshore structures. By manipulating factors related to boundary layers and their effect on drag, engineers strive to enhance performance efficiency and reduce energy consumption.
Consider these key aspects regarding boundary layers’ influence on drag:
- Boundary layer thickness: Thicker boundary layers result in increased skin friction drag.
- Surface roughness: Rough surfaces amplify turbulence within the boundary layer, leading to higher overall drag.
- Flow separation: When flow separates from an object’s surface due to unfavorable pressure gradients or adverse geometric features (such as sharp corners), significant increases in both form and induced drags occur.
- Laminar-to-turbulent transition: Transitioning from a laminar boundary layer to a turbulent one can cause a sudden increase in drag, known as the drag divergence phenomenon.
By comprehending the dynamics of boundary layers and their effect on drag force, engineers aim to develop strategies and techniques to reduce overall resistance. In the subsequent section, we will explore various approaches employed in practice for minimizing drag forces and enhancing floating object performance.
Reducing Drag: Strategies and Techniques
Section H2: ‘Reducing Drag: Strategies and Techniques’
Building upon our understanding of the boundary layer and its influence on drag, we now turn our attention to exploring various strategies and techniques used to reduce drag in hydrodynamic systems. By implementing these methods, engineers can optimize the performance of floating structures, resulting in improved efficiency and enhanced stability. To illustrate this, let’s consider a hypothetical case study involving a large offshore platform designed for oil exploration.
Strategies and Techniques for Reducing Drag:
-
Streamlining Shapes:
- Utilizing streamlined shapes that minimize flow separation is crucial in reducing drag. By designing structures with smooth contours, such as teardrop or airfoil profiles, the resistance encountered by the fluid can be significantly reduced.
- The use of computational fluid dynamics (CFD) simulations enables engineers to analyze different geometrical configurations before physically constructing prototypes, saving time and resources.
-
Surface Treatment:
- Applying specialized coatings or textures on surfaces can modify their interaction with water molecules. For instance, superhydrophobic coatings help repel water droplets, effectively decreasing skin friction drag.
- Micro-riblet patterns engraved onto submerged surfaces have proven effective at delaying flow separation along the body of marine vessels, thereby minimizing pressure drag.
-
Boundary Layer Control:
- Active control mechanisms like suction or blowing are employed to manipulate the characteristics of the boundary layer near surfaces experiencing high levels of drag.
- These techniques involve actively removing or introducing mass flow through small holes distributed across the structure’s surface, altering velocity gradients and consequently reducing overall drag.
Table: Comparison of Different Drag Reduction Techniques
Technique | Advantages | Disadvantages |
---|---|---|
Streamlining | Significant reduction in drag | Limited applicability |
Ease of implementation | ||
Surface treatment | Decreased skin friction drag | Maintenance requirements |
Cost-effective solution | Limited lifespan | |
Boundary layer | Efficient control of flow | Requires energy input |
manipulation | Reduction in pressure drag | Complex implementation process |
Emotional Response
- Enhanced efficiency and stability lead to cost savings and improved environmental sustainability.
- Cutting-edge technologies enable engineers to optimize performance and reduce the ecological footprint of hydrodynamic systems.
- Innovative approaches not only enhance operational effectiveness but also contribute to scientific advancements in fluid dynamics research.
- By implementing these strategies, industries can stay competitive while minimizing their impact on natural resources.
In summary, through streamlining shapes, surface treatment methods, and boundary layer control techniques, engineers have a range of options for reducing drag in floating structures. These strategies not only improve performance but also promote sustainable practices within the industry. As technology continues to advance, it is crucial that we embrace innovative solutions that maximize efficiency while minimizing our environmental impact.